At Active-PCB Solutions, we’ve just invested in our third reflow oven – a BTU Pyrammax 100A convection air reflow oven – to bring the capability of lines 1 and 2 to our third assembly line.
Reflow ovens have significantly evolved over the past two decades. They’re no longer just machines that heat a board and its components to melt solder.
But what are modern reflow ovens and what is their role in PCB assembly?
Surface mount technology (SMT) has become the standard for assembling compact, high-performance printed circuit boards. At the heart of the SMT process is surface mount soldering, a method that requires a precise and controlled application of heat to form reliable electrical connections. One of the most critical tools used in this process is the reflow oven.
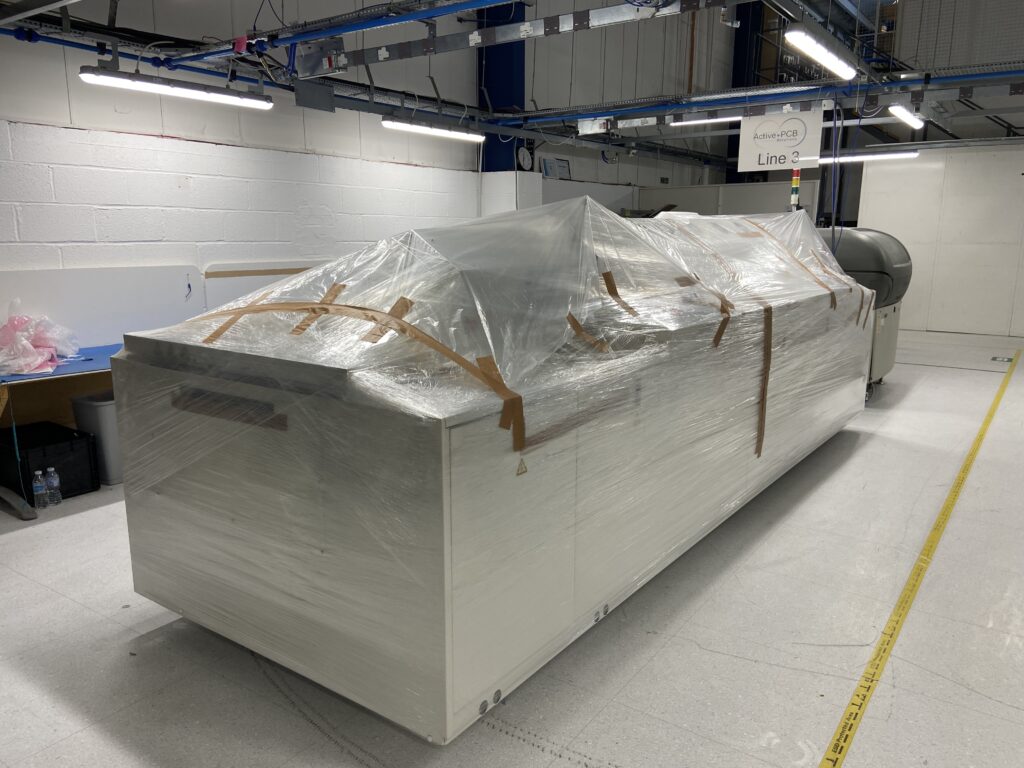
Today, reflow ovens are advanced, data-driven systems that play a central role in ensuring the quality, efficiency and repeatability of the surface mount soldering process. At Active-PCB Solutions, we use the latest reflow oven technology to deliver consistent, high-reliability assemblies for a wide range of industries.
What Is Reflow Soldering?
Reflow soldering involves applying solder paste to the pads of a printed circuit board, placing surface mount components onto the paste, and then heating the entire assembly in a reflow oven. The oven melts the solder, creating a permanent bond between the component leads and the board. The process must be tightly controlled to ensure proper wetting, joint strength, and long-term performance.
A typical reflow oven is divided into multiple temperature zones that create a thermal profile. These zones include preheat, soak, reflow and cooling. The board passes through each zone on a conveyor system. The temperature profile is critical, as different components and board materials have varying thermal tolerances. A poorly designed profile can lead to cold joints, damaged components or warping of the board.
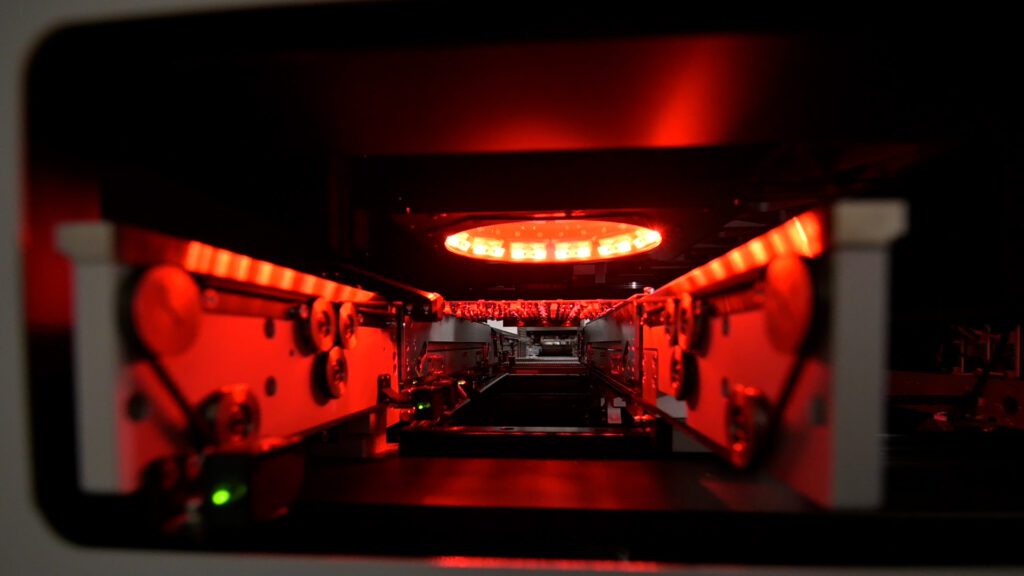
The Advantages of Modern Reflow Ovens
Modern reflow ovens can offer a wide range of features that improve quality and efficiency. Multi-zone temperature control allows for fine-tuned thermal profiling, ensuring uniform heating across the entire assembly. Advanced profiling software provides real-time monitoring and adjustment of the heat curve, reducing process variation and allowing engineers to dial in the exact conditions needed for each assembly type.
Another important advancement is the use of nitrogen reflow environments. By reducing oxygen levels in the oven, oxidation of the solder and component leads is minimised. This results in cleaner joints, improved wetting and enhanced long-term reliability. Nitrogen reflow is particularly useful in high-reliability applications such as aerospace, automotive and medical electronics.
Energy efficiency has also improved significantly. Newer reflow ovens are designed with better insulation, lower power consumption and smarter heat recovery systems, making them more cost effective to operate and more sustainable. Combined with reduced rework and scrap rates, these improvements contribute to a leaner and more eco-friendly manufacturing process.
Reflow Ovens Improve Surface Mount Soldering Quality
Reflow ovens directly impact the quality of the solder joints, which in turn affects the performance and lifespan of the final product. By delivering consistent and repeatable heat profiles, modern ovens help ensure each joint is formed correctly, reducing the chances of issues such as tombstoning, bridging or voiding.
Additionally, integrating reflow ovens with automated inspection systems such as our AOI (Automated Optical Inspection) machine allows for closed-loop feedback and process correction. This helps identify and eliminate defects early, resulting in higher first-pass yields and improved customer satisfaction.
The Active-PCB Solutions Approach
At Active-PCB Solutions, we invest in high-specification reflow ovens. This technology, combined with our skilled engineering team and rigorous quality systems, ensures that each board we produce meets the highest standards. Whether we are working on low-volume prototypes or high-mix production runs, the reflow process is a critical part of our commitment to excellence.
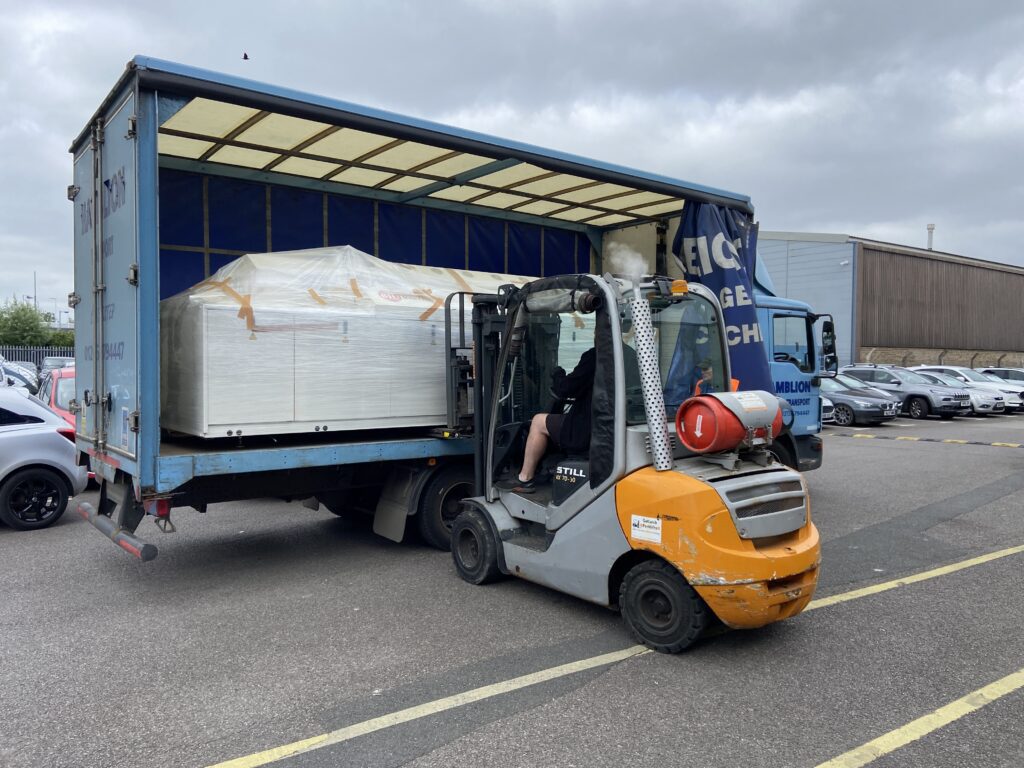
Surface mount soldering continues to evolve, and reflow ovens remain at the centre of that evolution. As component sizes shrink and board complexity increases, the demand for precise, reliable soldering grows. Reflow ovens are no longer just part of the process; they are enablers of quality, efficiency and innovation in electronics manufacturing.
If you are looking for a manufacturing partner that understands the value of process control and invests in the right technology, we would be happy to speak with you. Contact us to see how we can turn your ideas into a reality.