Printed Circuit Board (PCB) design is no longer just about placing components and routing traces. At Active PCB, PCB design is about anticipating the full lifecycle of a product, from prototyping to production – to use in the field, and beyond. That’s where the concept of Design for X (DfX) comes into play.
Designing for X is a methodology that reduces the overall cost, accelerates the time to market and enhances the quality of the electronics and the user experience.
At Active-PCB Solutions, we believe integrating Design for X into PCB design is essential for delivering smarter and more reliable solutions for our clients.
So, What is Design for X?
Design for X is a catch-all term where ‘X’ can stand for various quality and performance goals. This could include Design for Manufacture (DfM), Design for Test (DfT), Design for Reliability (DfR), Design for Procurement (DfP)and Design for Cost (DfC), etc.
These principles guide engineers to consider downstream processes early on in the design phase, making layout and component decisions that align with manufacturing capabilities, ease of testing, environmental durability, and cost targets.
It is about using expert knowledge and taking the time to be proactive, think ahead and get things right, first time.
Why does DfX Matter in PCB Design?
A PCB designed with only the electrical performance in mind can fall short during fabrication or assembly. This can lead to several prototype iterations and costly redesigns.
By adopting Design for X, Active-PCB proactively address challenges including:
- Design for Manufacturability (DfM): Ensuring trace widths, via sizes, and spacing meet fabrication tolerances to prevent delays or defects.
- Design for Testability (DfT): Including test points and accessible signals to enable easier validation and fault detection.
- Design for Reliability (DfR): Choosing components and materials suited to thermal, mechanical, and environmental stressors.
- Design for Assembly (DfA): Aligning component orientation and spacing with pick-and-place machine capabilities to streamline production.
- Design for Cost (DfC): Balancing performance and material costs without sacrificing quality.
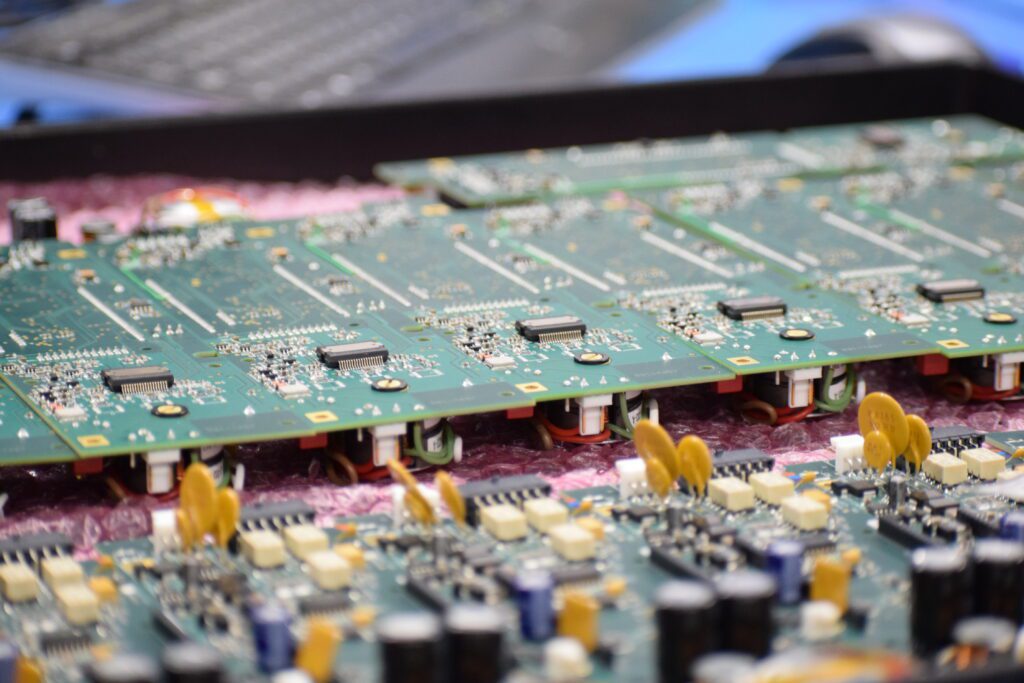
Our Approach to Design for X at Active-PCB Solutions
At Active-PCB, our engineering team work closely with clients to incorporate Design for X from the very beginning of every new project.
By leveraging state-of-the-art design tools and our years of manufacturing knowledge and experience of PCB design, we help ensure that every PCB is optimised not just for function, but for every step that follows.
Our collaborative process includes:
- Early design reviews conducted between experienced staff and the client, to align on manufacturing constraints.
- Feedback loops with the production staff to identify any unanticipated sticking points or possible future efficiencies.
- Risk assessments to identify potential failure points.
- Cost modelling to support budget-conscious decisions.
Design for X isn’t just a buzzword; it’s a mindset that governs the PCB design process. When applied from the beginning of a project, DfX leads to more robust products and faster turnaround times, and means greater overall value for the customer.
At Active-PCB, we don’t just build printed circuit boards. We build partnerships which are grounded in intelligent design, precision manufacturing, and our ongoing commitment to excellence.
If you’re to optimise your next PCB project with DfX principles then contact us today to get started.